What is the difference between SLA and SLS?
When choosing a 3D printing or additive manufacturing process there is a lot to consider – here we revisit SLA and SLS. Tim wasn’t wrong in his last article on SLA vs SLS when he said it’s all about trade offs!
The development of SLA and SLS dates back to the early 80’s. Following this, the first commercial SLA systems were released 1986 by 3D systems. In the early 90’s the first SLS systems were commercialised by DTM, which later became part of 3D Systems. The point of this history lesson you ask? Really to emphasise how much additive manufacturing has evolved with over 20 years of industry experience. We are in a place where technology and materials have been tried, tested and well refined over the years.
What is the difference between SLA and SLS?
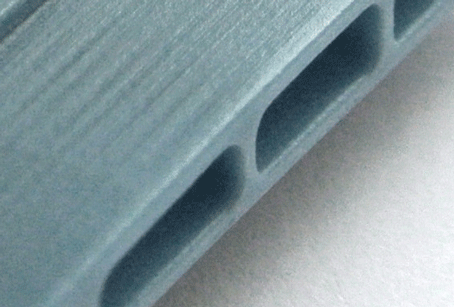
So, what is the difference between SLA and SLS? There are some common denominators, for example, both use a laser to trace out and build individual layers. For SLA a liquid resin is cured, whereas in SLS powder is selectively fused together.
Comparing the techniques isn’t easy as they both have pros and cons. If we were limited to a single sentence summary, it would have to be that SLS is generally tougher and lower in cost, whilst SLA produces parts with tighter dimensional tolerances and have a better surface finish more akin to injection moulded parts. However once we start looking in more detail, choices will then start coming down to individual project requirements.
Feature definition
If feature definition is a consideration, SLA is generally better able to produce small and well-defined features. There are also high-resolution SLA systems designed for smaller parts. The definition of small features with SLS is slightly hindered by the powders grainy surface appearance.
Feature sizes
Feature sizes are roughly comparable on paper but SLA probably has the edge in reality, especially if high resolution SLA is considered, as shown below.
Feature |
SLA |
SLA (high-res) |
SLS |
Build Volume | 1500x650x550mm (max) | 250x250x250mm (commonly)
380x380x250mm (possible) |
550x550x750mm or
700x580x380mm |
Thin walls | 0.6-0.8mm | 0.2mm | 0.8mm |
Holes | 0.8-1.0mm | 0.5mm | 0.8-1.0mm |
Clearance Space (in other words, to avoid joining) | 0.6mm | 0.4mm | 0.3mm |
Whilst SLA might be better for small features – SLS has the advantage over SLA in that the surrounding powder provides support to the parts during the build process. For SLA, parts either need to be designed to be ‘self supporting’ or additional support structures need to be built to support the part during the process. Note however, this will add time and cost due to post processing. With SLS the powder supports the part, allowing complex geometries and channels to be built which might not be possible to build without supports in SLA.
There is a common misconception that SLS parts are porous, but actually water absorption values quoted in data sheets range in the order of 0.1-0.5%. The surface of the part is likely to be water absorbent due to the powdery surface finish, but this doesn’t mean the whole part is.
Post Prosessing
Both SLA and SLS require post processing. SLA parts need to be cleaned to remove un-cured resin, undergo a post cure, and supports need to be removed. With SLS, excess powder needs to be removed. Both processes are relatively well matched on the ability to be machined, sanded and painted to achieve good surface finish and remove evidence of layers.
Commonly used materials
Here is a summary of some of the commonly used materials.
Requirement |
SLA |
SLS |
PA | DuraForm
DuraForm Ex PA2200 PA2201 |
|
PP-Like | Accura 25
Somos 9120 |
PP-Like SLS |
ABS-Like | Accura 55
Renshape SL7565 |
|
High(er) Temperature | Accura Bluestone
Accura CeraMax Somos Perform Somos Nanotool |
DuraForm Glass Filled
DuraForm HST 3200 Glass Filled |
Clear | Accura ClearVue
Accura 60 Watershed Renshape SL7565 |
N/A |
Flexible | N/A | DuraForm Flex |
Please speak to us if you would like to know more about more specialist materials eg SLSPeak, SLAPeak, SLSCarbon or SLAhigh-res.
For specific material properties take a look at our data sheets here.
SLA v SLS – who wins?
So yes, it’s all about the trade off and this is often project specific. Both might be used in one project – for example we may opt for SLS as a first prototype to keep costs down, and then choose SLA for the final prototype for a better surface finish. The clear winner in this race is the end user as competition between the two methods drives forward developments in technology and new materials.